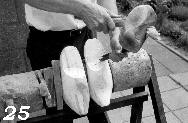
Boring,
also
called parbuckling, is the hardest part for a wooden shoe
maker. The profession of making wooden shoes stands or falls
with a well fitting wooden shoe.
Every wooden shoe maker used to have his own models: high or
low, with a round or pointed nose, with a straight or curled
nose. But whatever model he created, its fitting should (and
shall) be always proper.
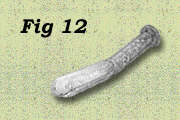
As
shown above, the first step is to make a well fitting hole
for the heel of the foot. For this the wooden shoe makers
uses a gouge as shown in fig. 12.
This was the first task an apprentice (about 12 years old)
got to perform. This had a good reason: Making wooden shoes
by hand is hard work. This very first part was the easiest and
therefore could be well done at an early age in former days.
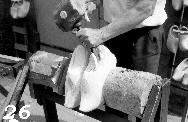
The process is as follows: The gouge is struck into the wood
along the hood, as shown on photo 25. Not too deep and under
a small angle. This is to avoid that the hood cracks in this
early phase. Then the gouge is placed at the top of the heel
and the wooden shoe maker starts gouging (photo 26).
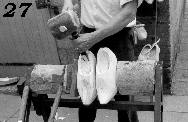
With every stroke, he tugs a little to prevent that the
gouge gets stuck. With every loose chip he turns the gouge
so that he can cut the chip from the wood. By doing that,
the hood doesn't tear off. This is the way the first wood is
removed.

When the hole for the heel is large enough, a
large drillknife is used to finish the hole (fig. 13)
This
tool is again wielded in a totally different way than the
previous ones. An aspect that makes this profession so
fascinating.
This phase of boring out the hole should be performed very
precisely. It determines the maximum thickness of the heel,
but also the maximum depth of the wooden shoe and thus the
overall fitting. It requires a lot of strength.
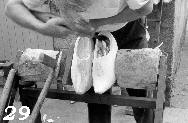
As shown on photo 29, the wooden shoe
maker uses his complete fore-arm. This is necessary because
boring needs to be done "out of the hand". For he can't let
the shaft of the knife lean on the edge of the wooden shoe
because it will then tear off. By scooping out the wood he
creates sufficient space inside the back of the wooden shoe.
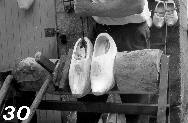
Such a drill is also called a scoop or
spoon. Several types exist: The large scoop, the chasing
drill and the large and small spoon. The described
application of these drills is simply called
drilling in Limburg (a
southern province of Holland). In other areas of Holland
like in Brabant or De Achterhoek it's called
parbuckling. (Dutch
words are
uitheulen,
uitboren and
schrooien).
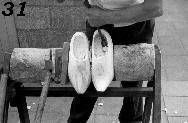
In particular notice the manual exercises and grips needed
to wield the drills. The wooden shoe maker stops with these
tools if he has created enough room inside the wooden shoe.
If necessary, the edge can be touched up a little
afterwards.