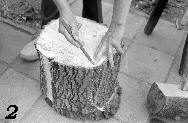
Before the wooden shoe maker cleaves or
splits a log, the log is measured again. This concerns the
length and diameter of the log. Then the log is inspected
for faults and possible changes of color that indicate that
a branch has been cut or has been blown off, even if it
happened years ago. Then he inspects the bark. When it looks
coarse, this means that cleaving the wood is difficult. The
necessary blocks are measured more largely, more broadly, in
proportion to the coarseness of the bark. A block of wood as
shown on photo 2, is not easy to split. In that case you can
use the following strategy:
- Assume that a log has a length of 33 cm and a
diameter of 35 cm.
- The perimeter equals 3.14 x 35 = 110 cm.
- Every log of this length needs a thickness of
20 + 2 = 22 cm
(2 cm extra to cover cleaving difficulties).
- When there are no internal faults, then 5
usable blocks come out of this log (see also
fig. 4).
|
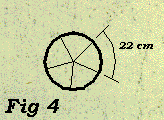 |
Cleaving or splitting a log is done using a cleaving hammer and two chisels (fig. 5).
Two chisels are used because cleaving is often done in a
certain angle (e.g. in the case on photo 3, where 5 blocks
reside in a log). Wooden shoes that are being constructed
from cleaved wood (instead of sawn wood), can be a little
thinner, and therefore lighter. Despite the fact that their
walls are thinner, they are even stronger because the thread
of the wood is never crossed. The wood is also more flexible
and elastic, this is exactly the reason why often handles of
hammers and spades also are cleaved.
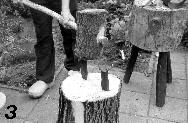
Remark: The careful observer will notice that on photo 4,
on the lower left side of the bark, a small distortion is
visible. This distortion indicates that an inner knot is
present. The wooden shoe maker will incorporate this knot
in the floor of the wooden shoe and later on, during the
"uptoeing" phase, this knot will then drop off completely.